Custom DCPD, RIM, and RTM Molding
Osborne’s specialty in the custom molding of thermosetting plastics and composites has been helping leading companies across the U.S. solve their toughest plastics challenges for more than 50 years. Fully customized RTM (Resin Transfer Molding) and RIM (Reaction Injection Molding) capabilities provide us with the flexibility to meet virtually any customer-specified requirement.
Osborne Industries brings more than 50 years of practical production experience to offer you the full advantages of custom thermoset molding via Reaction Injection Molding (RIM) and Resin Transfer Molding (RTM). Whether it’s a custom resin formulation or the capacity of large projects, Osborne will customize the design and final product to your exact specifications.
Customers for custom thermoset molding services at Osborne range across a variety of industries, each with a unique set of materials and part specifications. Generally, molding capacity ranges from 100-20,000+ parts per year and individual pieces range from 1-1,000 lbs. Let us provide you with the Osborne advantage for your next custom molding project.
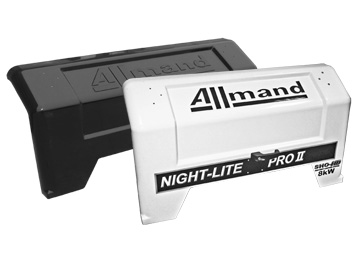
pDCPD MOLDING
Polydicyclopentadiene (pDCPD) is an engineered thermoset polymer possessing an excellent combination of chemical and corrosion resistance, stiffness, impact strength, and heat resistance utilized in the Reaction Injection Molding (RIM) process.
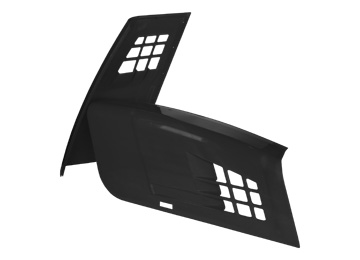
REACTION INJECTION MOLDING
Reaction Injection Molding (RIM) at Osborne provides a complete range of polymer material properties for virtually all applications at any volume - from testing new market concepts with low-cost composite tooling options to the production of 20,000+ parts per year.
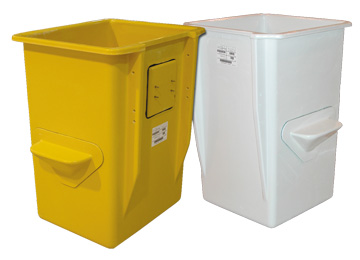
RESIN TRANSFER MOLDING
The closed-molding process of thermoset materials known as Resin Transfer Molding (RTM), was utilized and perfected by Osborne scientists and engineers in the 1970s, before the industry even had a name for it.